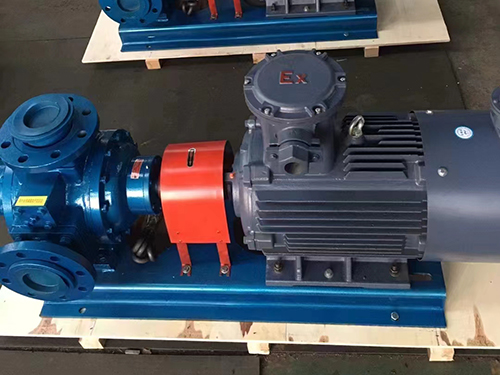
YQB sliding vane pump
Describe: YQB sliding vane pump is mainly used to transport volatile liquids with similar properties, such as liquid ammonia, ammonia water, methanol, dimethylammonium, epoxy propane, crude b...
TEL:+8615076761164
Email:amy.hypump@gmail.com
DESCRIPTION:
YQB sliding vane pump is mainly used to transport volatile liquids with similar properties such as liquid ammonia, ammonia water, methanol, dimethylammonium, epoxy propane, crude benzene, ethylene oxide, chloroform, isobutene, butadiene, etc. It is widely used in industries such as gas, petroleum, chemical, pharmaceutical, and metallurgy. The sealing ring and sliding vane of the pump are used in many regions, with high corrosiveness, toughness, and strength. The material of the pump casing is alloy cast iron with good density and corrosion resistance, After processing, the smoothness is high, thereby protecting the ammonia liquid from leakage. The characteristics of the pump are good sealing, high pressure, and stability.
Working principle of YQB sliding vane pump: This pump type is a positive displacement vane pump, which works by centrifugal sliding of the blades. The flow rate is related to the speed of the shaft. The inner surface of the stator is made of domestic composite curves, and the stator, rotor, baffle, and blades form ten sealed chambers. Due to the composite curve of the stator surface, when the rotor rotates, the chamber volume gradually increases and forms negative pressure to generate suction force, thereby inhaling ammonia liquid. When the rotor rotates at an angle, the volume gradually decreases, thereby pressing out the ammonia liquid. There is an oil block between the oil suction chamber and the oil pressure chamber to separate the oil chamber from the oil pressure chamber. The blades rely on centrifugal force and a two baffle structure to tightly adhere to the inner curvature of the stator, enabling the pump to operate normally at rated conditions.
The YQB sliding vane pump is composed of components such as the inner sleeve, rotor, shaft, sliding vane, and side plate. There is an eccentricity e between the inner sleeve and the rotor, and the sliding plate is placed in the rotor slot and can slide along the slot. When the rotor rotates, the sliding plate relies on its own centrifugal force to tightly adhere to the inner wall of the inner sleeve, forming several closed working chambers between the inner surface of the inner sleeve, the outer surface of the rotor, the sliding plate, and the end faces of the two side plates. When the rotor rotates counterclockwise, the right sliding plate gradually extends out, and the volume between adjacent sliding plates gradually increases, forming a local vacuum, The liquid enters the chamber through the suction port, which is the suction process of the pump. The sliding plate on the left is gradually pressed into the groove by the inner sleeve, and the enclosed volume between adjacent sliding plates gradually decreases, pressing the liquid out of the discharge port. This is the pumping process. Rotate the rotor once to complete one suction and one discharge. There is a sealing oil area between the suction and pressure chambers of the pump, which separates the suction and pressure chambers. The displacement Q of the pump is directly proportional to the eccentricity e and the pump speed n. Therefore, the displacement can be adjusted by changing the eccentricity and speed, or a series of products can be made to meet the needs of different working conditions.